Engineers at the California Institute of Technology have made a breakthrough in the field of nano and microarchitectural materials by creating a new material consisting of several interconnected microscale assemblies. Compared to structurally identical but unbonded materials, the presence of knots in this new material greatly increases its strength, allowing it to absorb more energy and deform more before returning to its original shape without being damaged. These new knotty materials may find applications in the biomedical and aerospace fields due to their strength, potential biocompatibility and extreme deformability.
“The probability of overcoming the general trade-off between material deformability and tensile strength [здатністю розтягуватися без руйнування] ex-Caltech alumnus offers new ways to design devices that are highly flexible, durable, and capable of operating in harsh environments,” says student Widianto P. Moestopo (MS ’19, PhD ’22), now at Lawrence Livermore National Laboratory. Moestopo, March 8′ He is the lead author of the paper on nanoscale assemblies published in Science Advances.
Moestopo helped develop the material in the lab of Julia R. Greer, Ruben F., and Donna Mettler, Professor of Materials Science, Mechanical and Medical Engineering; director of the Kavli Nanoscience Institute’s Fletcher Jones Foundation; and senior author of the scientific paper work . Greer is at the forefront of creating such materials with nanoarchitecture, or materials whose structure is designed and organized at the nanometer scale and therefore exhibit unusual, often surprising properties.
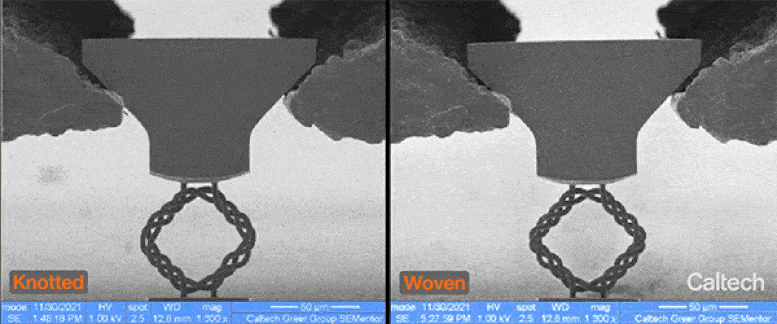
The tensile strength (right) of a material formed with micro-scale knots (left) compared to a knot-free but structurally identical material
“Beginning to understand how nodes would affect the mechanical response of microarchitectural materials was a new out-of-the-box idea,” says Greer. “For example, we have conducted large-scale studies of the study of the mechanical deformation of many other types of microtextiles, such as meshes and woven materials. By diving into the world of knots, we were able to gain a deeper understanding of the role of friction and energy dissipation, and this turned out to be important.”
The height and width of each knot are approximately 70 micrometers, and the radius of each fiber is approximately 1.7 micrometers (about one hundredth of the radius of a human hair). While these aren’t the smallest knots ever created – in 2017 chemists tied a knot made up of a single chain of atoms – it’s the first time a material consisting of multiple knots has been created at this scale. It also demonstrates the potential value of incorporating these nanoscale assemblies into a material, for example, for crosslinking or coupling in biomedicine.
Knotted materials formed from polymers exhibit tensile strengths significantly superior to non-knotted but structurally identical materials, including materials in which individual fibers are interwoven instead of knots. Compared to their non-knotted counterparts, knotted materials absorb 92 percent more energy and require more than twice the stress to burst when pulled.
The nodes are not tied but fabricated in a connected state using advanced high resolution 3D lithography that can create nanoscale structures. Examples described in the document Science Advancesincludes simple knots—an extra twisted top knot that provides extra friction to absorb extra energy when the material is stretched. The team plans to explore materials made from more complex assemblies in the future.
Mostopo’s interest in knots arose from research he conducted during the COVID-19 quarantine in 2020. “As opposed to knots in a purely mathematical sense, I came across several papers by researchers examining the mechanics of physical knots. I don’t consider myself a mountaineer, sailor, or mathematician, but I’ve been knitting knots my whole life, so I thought of including knots in my projects,” she says.